Are you looking to replace existing casters or add them as an accessory to some industrial equipment? With so many types of industrial casters available, choosing can be difficult, especially for the first-time buyer.
Where do you even start? Does the material of the caster make a difference? What’s the difference between polyurethane and polypropylene wheels? Do you need steel or cast iron wheels? What’s a heavy-duty caster, and do you need one? – This article has all the answers to your questions.
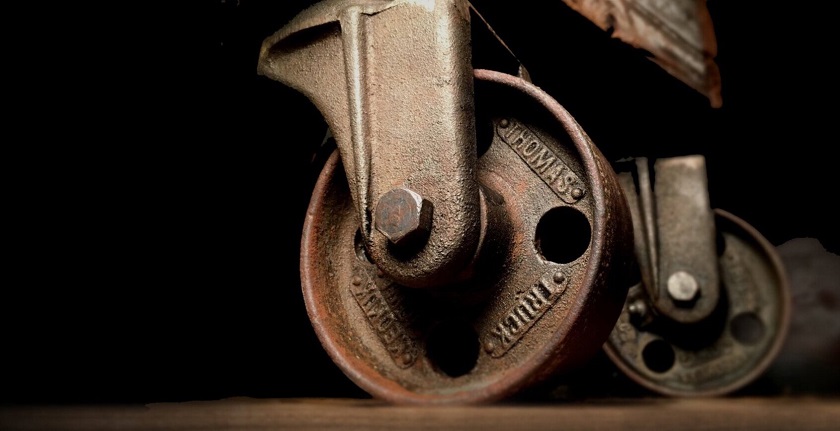
What Are Casters and Wheels?
Castors and wheels can be placed on many pieces of equipment to make it easier to transport and move them around. They’re generally placed on theatrical seats, gates, trolleys, street sweepers, amusement park rides, kitchens, cleaning rooms, greenhouses, airports, etc. – the options are limitless. The castors contain a wheel and the assembly unit so you can attach them to the item you want to move.
Standard castors have wheels that spin on an axle. As a result, they allow for only lateral movement. However, if you need more than lateral movement, you can get swivel casters that can move in any direction.
There are two types of industrial casters you can buy – single bolthole and plate casters. Single bolthole casters are limited to loads of 0.5T and feature a fastener through the centre of the swivel head. Plate models, on the other hand, have a flat bracket with four mounting holes that allow the load to be evenly spread. Both single bolthole and plate models can be swivelled, fixed and swivel braked.
Both types of casters are available in a range of materials, including stainless steel or zinc plated, and have varying load-bearing capabilities that are suited for different uses in different environments.
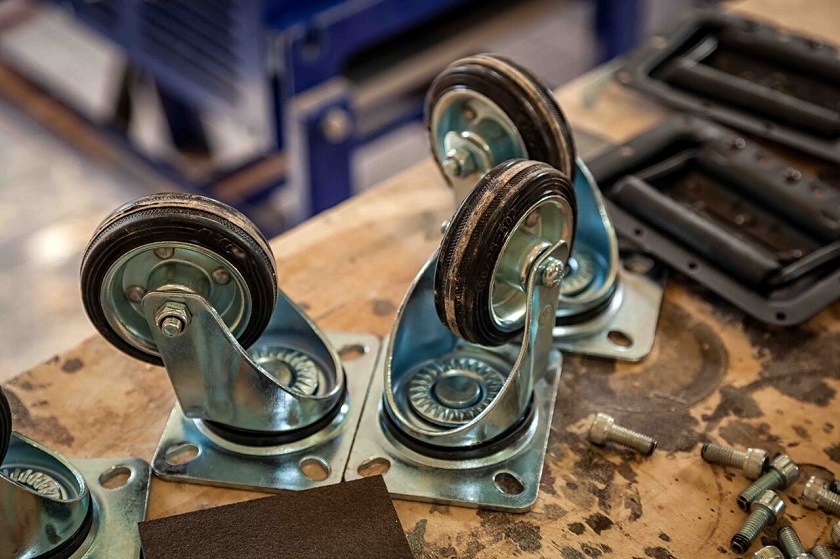
Where Are Casters and Wheels Used?
As aforementioned, virtually everywhere! Offices, the catering industry, homes, motoring and aerospace industries, warehouses, logistic centres, distribution and manufacturing centres, hospital labs, pharmaceutical industry, retail and furniture industries, mailrooms, sports centres, filmmaking industries and so on.
Choosing the Ideal Casters and Wheels
There are various parts that makeup casters, and not all casters are created equal. The construction and the wheel are two factors to consider because they determine whether the solution will be satisfactory for the task at hand or a letdown. You’ll avoid making a costly error if you are aware of the following things when choosing the right caster and wheel.
Load-Bearing Capacity
The load-bearing rating of castor varies based on the type and material they’re made from. They’re designed to support a specific load and it’s important to stay within this limit for safety reasons and to avoid damaging the castors and whatever you’re carrying or moving.
Depending on the weight of the equipment, there are light-duty and heavy-duty models from which to choose. Light-duty wheels are suitable for weights up to 125 kg. On the other hand, if you need to move something that weighs more than this, heavy-duty models can withstand loads up to 500 kg.
Make sure the condition of the surface on which you use the castors is also taken into consideration. Cracked surfaces or surfaces with uneven joints or gullies can add extra loading onto the castors. This is because some of the castors may lose contact with the surface, meaning the extra load will fall on the other castors.
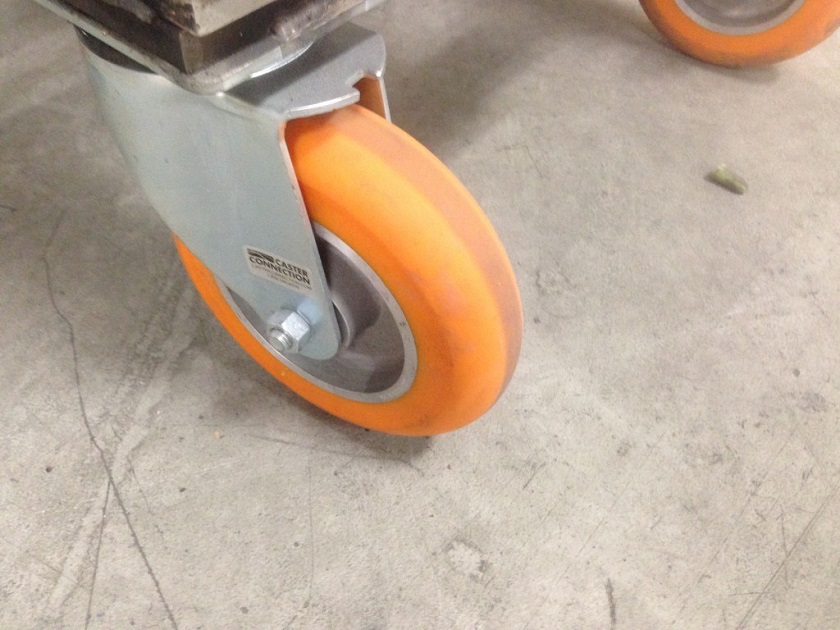
Environment Conditions
When it comes to the environment and the moving surface, you need to consider the type of wheels. For instance, bouncy, stretchy wheels help you move on surfaces with obstacles. Therefore, wheelbarrows and other machinery used on uneven terrain come with pneumatic or rubber wheels.
What’s more, working in environments with chemicals can damage the castors unless they’re made of appropriate materials to handle them. Corrosive chemicals like oils and acids can easily damage rubber castors Pressed steel and polyurethane, on the other hand, can resist these just fine.
Some manufacturers rate their castors on a scale from A to F, with A-rated castors being the most chemical resistant. The rating is based on how long the castor can withstand being immersed in the chemical before it starts getting damaged.
Moreover, the rating refers to the entire wheel assembly, not just the tyre. Some wheels and tyres can withstand certain chemicals easily and might be unsuitable for use in other environments. For instance, cast iron is resistant to plant and mineral oil-based chemicals but prone to damage from acids.
Mounting Castors on Equipment
When replacing existing castors, you can use the mounting already present. In that case, you’ll simply need to know the load capacity required of the castors. For single bolt-hole mounting, loads are limited up to 500kg. For plate mounting, you’ll also need to consider the width and length, the number of holes and the spacing between them.
There are industry standard sizes between which you can choose. Plate mountings are generally more robust and the preferred choice if there’s enough room to attach them. They provide more stability, can take greater loads and come in various sizes.
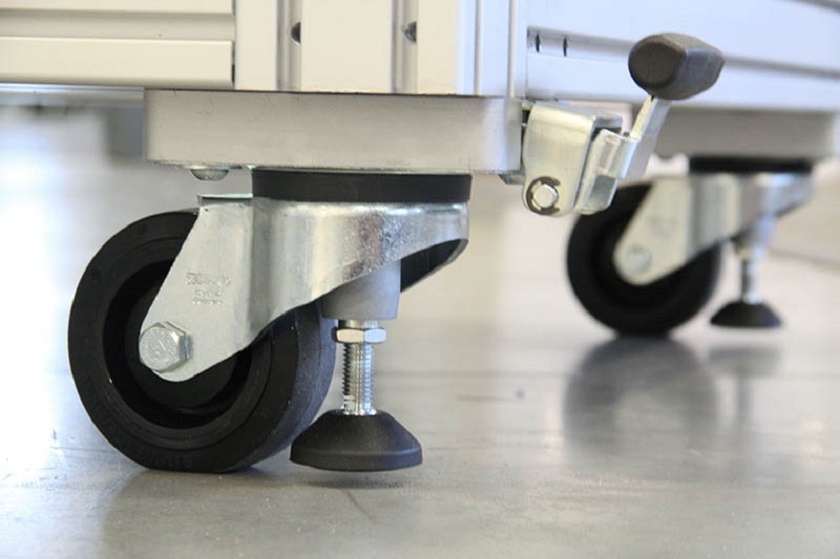