Welding is an essential process in a wide range of industries, as well as DIY and home improvement projects. If you’re looking to buy your first welding machine, there are a few different things to consider, including your welding skills, the different welding processes, and the capabilities of each welder machine.
Once you understand your needs and your choices, you can easily determine which welding machine is best suited for you.
Types of Welding Processes
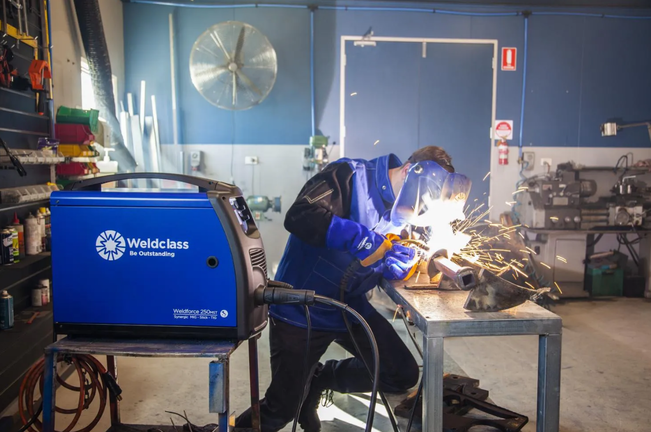
Gas Metal Arc/MIG
MIG welding, also known as gas metal arc welding utilises a wire welding electrode on a spool fed at a pre-selected speed. The arc is created with the help of an electrical current between the wire and base metal. The wire is melted and joints with the base, producing strong welds that look good and require little to no cleaning. MIG welding is relatively easy to learn, and is appropriate for both thick and thin metals. It works well with steel, stainless steel and aluminium, creating very clean welds.
Similar to MIG welding is flux-cored arc welding. Here, a wire is also fed, but unlike MIG welding, you don’t need shielding gas. Instead, the wire itself shields the arc from any contamination. This is an even simpler process, yet it’s highly efficient, and is typically recommended for outdoor use, when welding dirty materials and in unfavourable conditions. It’s the go-to process for many construction applications due to its high speed and ease of portability.
Gas Tungsten Arc/TIG
TIG welding utilises a tungsten electrode that isn’t consumable to produce the weld. The welding area is guarded against contamination by argon shielding gas and filler material. However, some welds, called autogenous welds, don’t require any of this. With the help of a column of ionised gas and plasma, energy is conducted throughout the arc using a constant current. With TIG welding machines, you can weld thin stainless steel, alloy steel and non-ferrous metals such as copper, magnesium and aluminium. It allows for superior control over the weld, consequently producing high-quality and extremely durable welds. However, it’s more complex than other welding processes and is considerably slower.
Shielded Metal Arc/Stick
This is the most popular welding process used for non-professional use. It utilises an electric current that flows from a gap between the arc welding electrode and the metal welded. It’s an effective welding method for most joints and alloys, and it can be used in any type of setting. It’s economical, and capable of creating great bonds on dirty and rusty metals. However, you can’t weld metals thinner than 18 gauge and it requires quite a bit of cleaning once finished. Additionally, it requires rod changing. Stick welding is difficult to use and learn, especially when it comes to maintaining an arc. There are many types of stick welding machines, including AC, DC, AC/DC. All of these welders are great for hobbyists, farmers and home improvement projects.
Key Factors to Consider When Buying a Welder
The type of welder you buy should be suited for the projects you think you’ll work on. Think about what your goals are and consider whether you’ll need to weld anything else outside of those projects. Moreover, consider whether you’ll want to pick up any other processes in the foreseeable future. It’s important to consider the power and amp requirements, and take things like duty cycle into account in order to ensure you get the best welds and the most economical operation.
Besides the welder, consider the cost of the accessories and consumables as well. The consumables are an ongoing cost that you’ll have to keep paying for down the road. So, don’t feel pressured into making a fast buying decision. Take the time to think it all through, define your needs and get all your questions answered by an experienced welder. You can find all the information you need online.
FAQ About Welders
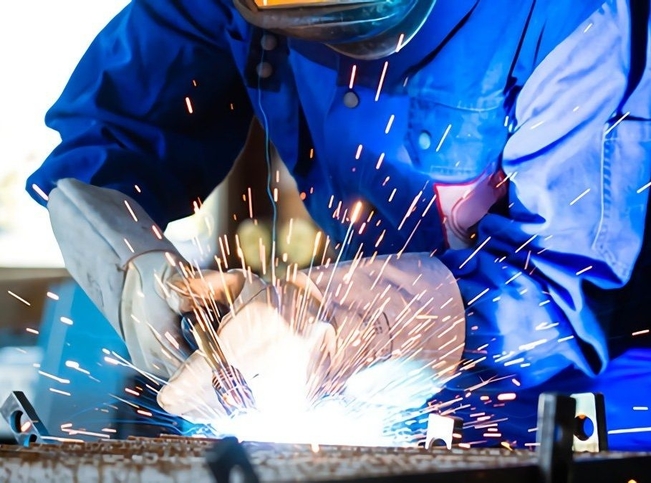
How many amps do I need?
Generally, you’ll need 1 amp for every 25 micrometres of metal. So, if you’re welding a material that is 1mm thick, you’ll need a welder with 40 amps.
What does the duty cycle represent?
The duty cycle refers to the time out of a 10 minute period the welder can operate before it overheats. So, let’s say you see a welder rated with a 60% duty cycle. It means that the welder can operate for 6 minutes, and then will require 4 minutes to “cool down”. However, keep in mind that when welding at lower outputs than the capabilities of the welder, the duty cycle can increase, and vice versa.
How much duty cycle do I need?
It depends on the application. In a home garage or shop setting, a welder with a lower duty cycle will probably be good enough to handle any task, since you’re probably welding at lower amps and stopping more often. However, if the welder is going to be used in manufacturing, fabrication or construction, where it’s going to be used at higher amps and more often, you’ll want a machine with at least 60% duty cycle.