Clamps are among the most valuable and commonly used tools by welders. And with a myriad of welding clamp types to choose from, the most crucial and most commonly overlooked of these clamps are the ones used for grounding.
Grounding clamps are responsible for maintaining a stable electrical path for striking clean, consistent welding arcs. More importantly though, in the event of a welding machine fault, grounding clamps provide the most direct route to earth to protect welding machine operators from electrical shocks that could be fatal.
That’s why when inventorying and verifying the safety of their tools, welders and metal fabricators need to pay as much attention to their grounding clamps as they would any of their individual articles of PPE, or the welding machine’s own thermal overload protection.
Discover Safer Welding With Magnetic Grounding Clamps
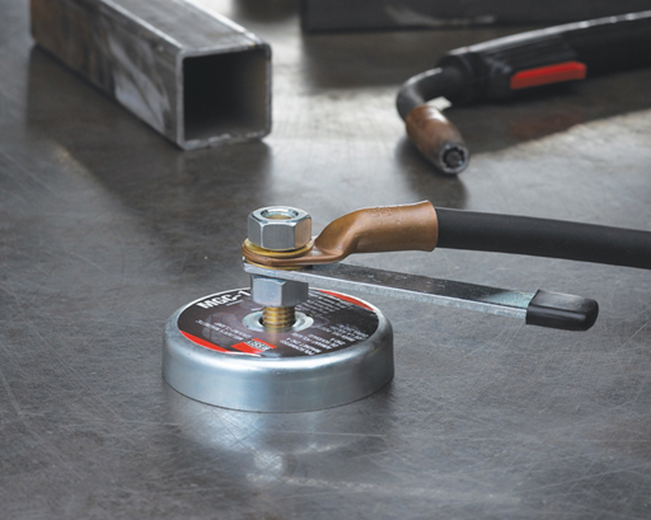
Let’s be honest: as metal fabricators are routinely faced with a long list of safety concerns that include everything from poor joint penetration to the possibility of fire or explosion, they don’t have time to ponder the reliability of their grounding clamps. That’s why solid gripping welding magnetic clamps are irreplaceable for worry-free grounding with any metal fusing project.
Magnetic clamps are easy to connect and disconnect and provide a positive, uninterrupted circuit every time a welder strikes an arc. And the fact that they can be used with all types of welding processes, including stick, TIG and MIG, gives them universal flexibility on any application up to their approved amperage rating.
Everything from the composition and thickness of a working piece, to the type of shielding gas and filler used has an effect on both the amperage a welder produces and the amperage it needs to produce. And as the duty cycle ranges on heavy duty 3-phase welding rigs are capable of exceeding 1,000A, adjustable magnetic welding clamps are safety critical for helping prevent the following:
- Potentially lethal electric shocks. With no-slip magnetic grounding clamps, metal fabricators can be confident that they’re protected from ungrounded currents that won’t hesitate to pass through any uninsulated conductor as it seeks a path to ground.
- Combustible and explosive hazards. Not only does the stable contact area occupied by a magnetic welding ground clamp help ensure increase weld strength, it also reduces the likelihood of arcing, or any type of unstable ground that could cause a fire or explosion.
- Catastrophic welding machine damages. A robust magnetic welding clamp dramatically reduces the risk of welding machine damages due to overheating, arc wandering (also known as arc blow) and even the possibility of the machine attempting to ground itself on the nearest unintended surface.
Heavy-duty magnetic welding clamps are typically sold individually or in packages of five, with individual ratings of 300A, 500A, and 600A each. They can also be combined to double and even triple their allowable amperage in either multi-cable grounding combinations, or when grounding multiple welders to a single working piece.
Quality Construction Is the Key to Magnetic Clamp Conductivity
The key to high-quality, industrial grade magnetic ground clamp assembly construction is materials. That’s because in addition to their naturally strong holding power, they also need to be incredibly durable and highly conductive. These are key qualities in any welding environment, but they’re especially important for magnetic welding clamps used in professional welding operations where their safety characteristics are clearly outlined in Australian Standards (AS) 1674.2.
It’s important to remember that when it comes to safety and reliability, every welding magnetic clamp has to be evaluated as a complete assembly. The hazards of working with compressed gases, and the prolonged exposure to heat and radiation mean that in spite of their simplicity, every magnetic clamp’s constituent parts have to be made for maximum longevity and conductivity. With the specialised clamp, you can benefit from:
- A corrosion resistant body. An annealed, stainless steel outer casing ensures maximum conductivity and minimal resistance, without being susceptible to corrosion or physical damage.
- Superior strength magnets. Fused composites like ferrite and forged, permanently magnetised metals like nickel-plated neodymium are the materials of choice for magnetic clamps, and are recognised for their strong holding power and stability at all temperatures.
- Highly conductive clamping hardware. Premium grade magnetic welding earth clamp assemblies utilise stainless steel and brass tube fastening hardware which, along with their highly conductive bodies, excel at enabling maximum current flow.
With their large contact areas and strong gripping power, some magnetic earthing clamps are also manufactured in swivel connector configurations. These extra versatile magnetic variants use oval point screws to secure their grounding cables, giving fabricators the freedom to maintain a strong ground from any angle, as well as the ability to quickly connect and disconnect from a clamp if it’s attached to a welding table or bench.
Magnetic Welding Clamps Drive Across the Board Operational Increases
While it’s easy to identify the risks that inadequate grounding poses to welders and welding machines, the danger of damaging a working piece is equally daunting. Whether it’s filling pinholes in car mufflers, joining oilfield pipeline or making CASA-approved airframe repairs, weld joint integrity is tied directly to how well the working piece is grounded when the welding is being done. This is where the gripping power of magnetic clamps proves its real value on the shop floor.
When compared with other types of clamps, the strong, wide-area clamping effort produced by magnetic clamps offers all the operational advantages that a welder or metal fabricator could ask for during the welding process, including:
- Increased flexibility. Magnetic grounding clamps can be used with any size or shape of working piece, eliminating the need to wrestle with spring- or screw-type clamps that can be difficult to attach, especially onto oversized working pieces.
- Increased weld strength. Not only does strong grounding contribute to increased weld strength, it also reduces the possibility of incomplete fusion and uneven heat distribution.
- Increased arc stability. Weld joint penetration depends heavily on arc stability, and the more positive the ground, the more stable the arc is when it’s struck.
The welding magnetic clamps cover all the angles when it comes to increasing throughput, and output quality. And together with their wide range of increases across the board, they won’t scratch, gouge, scuff the surface or finish of the working piece.
The Final Word
At the end of the day, regardless of the type of welding being done, if the grounding isn’t adequate, the results could be catastrophic. That’s why it behooves welders and metal fabricators to invest in the best possible grounding tools and equipment before a problem occurs. Solid gripping magnetic clamps are the answer for most earthing problems. They offer the safety and flexibility that metal workers need to strike every arc with confidence.